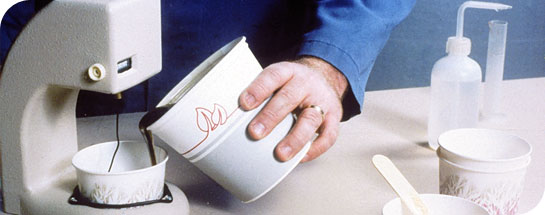
A-STAGE
An early stage in the preparation of certain thermosetting resins in which the material is still soluble in certain liquids, and may be liquid or capable of becoming liquid upon heating.
ACCELERATOR
An additive to polyester resin that reacts with catalyst to speed up polymerization. This additive is required in room temperature cured resins. See PROMOTER.
ACETAL PLASTICS
Plastics based on polymers having a predominance of acetal linkages in the main chain.
ACETONE
A ketone group solvent that is used to dissolve polyester resins. Used to a large extent for clean up of tools in fiberglass operations.
ACRYLIC PLASTICS
Plastics based on polymers made with acrylic acid or a structural derivative of acrylic acid.
ADDITION POLYMERIZATION
Polymerization in which monomers are linked together without the splitting off of water or other simple molecules.
ADIABATIC EXTRUSION
A method of extrusion in which after the extrusion apparatus has been heated sufficiently by conventional means to plastify the material, the extrusion process can be continued with the sole source of heating being the conversion of the drive energy, through viscous resistance of the plastic mass in the extruder.
ADDITIVE
Any number of materials used to modify the properties of polymer resins. Categories of additives include reagents, fillers, viscosity modifiers, pigments and others.
AGING
The effect on materials of an exposure to an environment for an eternal of time.
ALKYD PLASTICS
Plastics based on alkyd resins.
ALKYD RESINS
A polyester convertible into a cross linked form; requiring a reactant of functionality higher than two, or having double bonds.
ALLIGATORING
A visible cosmetic defect in the exposed gel coat which looks like wrinkled or alligator skin.
ALLOWABLE DEFECTS, VISUAL
The defects in non-critical areas which by nature, content, or frequency do not affect serviceability of the part are designated as allowable defects.
ALLOY
Two or more immiscible polymers united, usually by another component, to form a plastic resin having enhanced performance properties.
ALLYL PLASTICS
Plastics based on allyl resins.
ALLYL RESIN
A resin made by polymerization of chemical compounds containing the allyl group.
AMINO PLASTICS
Plastics based on amino resins.
AMINO RESIN
A resin made by polycondensation of a compound containing amino groups, such as urea or melamine, with an aldehyde, such as formaldehyde, or an aldehyde-yielding material.
ANTIMONY TRIOXIDE
Fire retardant additive for use with resins.
AROMATIC POLYESTER
A polyester derived from monomers in which all the hydroxyl and carboxyl groups are linked directly to aromatic nuclei.
ARTIFICIAL WEATHERING
Exposure to laboratory conditions, which may be cyclic, involving changes in temperature, relative humidity, radiant energy and any other elements found in the atmosphere in various geographical areas.
AVERAGE INJECTION VELOCITY
The mean value of the velocity of the molten plastic flow front within a cavity during the injection time that is calculated from the shot volume and injection time.
AUDIT
A systematic review to assess the implementation of prescribed procedures, specifications, or standards.
AXIAL
In the direction of the axis (Lengthwise centerline) of the equipment.
B-STAGE
An intermediate stage in the reaction of certain thermosetting resins in which the material swells when in contact with certain liquids and softens when heated, but may not entirely dissolve or fuse.
BAG MOLDING
An airtight film used to apply atmospheric force to a laminate." See VACUUM BAG MOLDING and PRESSURE BAG.
BARCOL HARDNESS
A measure of surface hardness made with a Barcol Impressor instrument in accordance with ASTM D-2583. The hardness value can be used as an indication of the degree of cure of FRP laminates.
BARRIER CREAM
A cream used to protect the skin from contact with resins.
BENZOYL PEROXIDE (BPO)
An initiator for curing polyester resin. BPO is used with aniline accelerators or where heat is used to cure the resin.
BI-DIRECTIONAL
Reinforcing fibers that are arranged in two directions, usually at right angles to each other.
BINDER
A resin soluble adhesive that secures the random fibers in chopped strand mat or continuous strand roving.
BIODEGRADABLE PLASTIC
A degradable plastic in which the degradation results from the action of naturally-occurring micro-organisms such as bacteria and fungi, and algae.
BLISTER
A flaw either between layers of laminate or between the gel coat film and laminate.
BLOCK COPOLYMER
An essentially linear copolymer in which there are repeated sequences of polymeric segments of different chemical structure.
BLOCKING
Unintentional adhesion between plastic films or between a film and another surface.
BLOOM
A visible exudation or efflorescence on the surface of a material.
BLOWING AGENT
A compounding ingredient used to produce gas by chemical or thermal action, or both, in manufacture of hollow or cellular articles.
BLOW MOLDING
A method of fabrication in which a heated parson is forced into the shape of a mold cavity by internal gas pressure.
BONDING
Joining of two or more parts by adhesive forces.
BOND STRENGTH
Force per unit area (phi) necessary to rupture a bond in interlaminar shear.
BRANCHED POLYENTHYLENE PLASTICS
Those containing significant amounts of both short-chain and long-chain branching and having densities in the 0.910 to 0.940g/cm3 range
BULK DENSITY
The weight per unit volume of a loosely packed material, such as a molding powder or pellets.
BULK FACTOR
The ratio of the volume of a given mass of molding material to its volume in the molded form.
BULK MOLDING COMPOUND (BMC)
A putty like mixture of any thermosetting resin containing fillers, fiber reinforcements, catalysts and thickening agents, or thermoplastic polymers, often extruded into logs or ropes.
BURNED AREAS
Areas of laminating showing evidence of decomposition (e.g. discoloration and /or cracking) due to excessive resin exotherm.
BURN OUT (BURN OFF)
Thermal decomposition of organic materials (resin and binders) from a laminate specimen in order to determine the weight percent of resin and glass reinforcement (synthetic reinforcements decompose together with the resin and binder).
BUTYLENE PLASTICS
Plastics based on resins made by the polymerization of butene or copolymerization of butane with one or more unsaturated compounds, the butane being in greatest amount by weight.
C-STAGE
The final stage in the reaction of certain thermosetting materials in which they have become practically insoluble and infusible.
CASTING
The process of pouring a mixture of resin, fillers and/or fibers into a mold as opposed to building up layers through lamination. This technique produces different physical properties from laminating.
CAST FILM
A film made by depositing a layer of plastic, either molten, in solution, or in a dispersion, unto a surface.
CATALYST
Technically considered an initiator, catalyst is the colloquial name given to the substance added to the resin or gel coat to initiate the cure.
CAULK
An elastic material used to protect joints or connections from external elements, particularly moisture.
CAVITY
The space between a male and female mold set in which the part is formed. Sometimes used to refer to a female mold.
CELL
A small cavity surrounded partially or completely by walls.
CELL, CLOSED
A cell totally enclosed by its walls and hence not interconnecting with other cells.
CELL OPEN
A cell not totally enclosed by its walls and hence interconnecting with other cells.
CELLULAR PLASTIC
A plastic containing numerous cells, intentionally introduced, inter- connecting or not, distributed throughout the mass.
CELLULAR STRIATION
A condition characterized by a layer within a cellular material that differs greatly from the characteristic cell structure.
CELLULOSIC PLASTICS
Plastics based on cellulose compounds, such as esters (cellular acerate) and ethers (ethyl cellulose).
CENTIPOISE
A unit of measure used to describe the viscosity of a liquid. Viscosity is measured with a Brookfield Viscometer for most polyester resin applications.
CHALKING
A surface phenomenon indicating degradation of a cosmetic surface. Chalking is a powdery film which appears lighter than the original color.
CHEMICALLY FOAMED POLYMERIC MATERIAL
A cellular material in which the cells are formed by gases generated from thermal decomposition or other chemical reaction.
CHIP
A small piece broken off an edge or surface.
CHOPPED STRAND MAT
A fiberglass reinforcement consisting of short strands of fiber arranged in a random pattern and held together with a binder. Mat is generally used in rolls consisting of 3/4 oz/ft2 material to 2 oz/ft2 material.
CHLORINATED POLY (VINYL CHLORIDE)
A poly (vinyl chloride) (PVC) polymer modified by additional chlorination.
CHLORINATED POLY (VINYL CHLORIDE) PLASTICS
Plastics based on chlorinated poly (vinyl chloride) in which the chlorinated poly (vinyl chloride) is in the greatest amount by weight.
CHLOROFLUOROCARBON PLASTICS
Plastics based on polymers made with monomers composed of chlorine, fluorine, and carbon only.
CHLOROFLUOROHYDROCARBON Plastics
Plastics based on polymers made with monomers composed of chlorine, fluorine, hydrogen, and carbon only.
CIRCUIT
In filament winding, the winding produced by a single revolution of mandrel or form.
CLOSED CELL CELLULAR PLASTICS
Cellular plastics in which almost all the cells are noninterconnecting.
CLOTH
A fiberglass reinforcement made by weaving strands of glass fiber yarns. Cloth is available in various weights measured in ounces per square yard or Kg/m2.
COLD MOLDING
A special process of compression molding in which the molding is formed at room temperature and subsequently baked at elevated temperatures.
COLLAPSE
Inadvertent desensification of cellular material during manufacture resulting from breakdown of cell structure.
COLOR STABILITY
The ability of a surface coating or pigment to resist degradation due to environmental exposure.
COMPOST
The product of composting.
COMPOSTABLE PLASTIC
A plastic that undergoes biological degradation during composting to yield carbon dioxide, water, inorganic compounds, and biomass at a rate consistent with other known compostable materials and leaves no visually distinguishable or toxic residue.
COMPOSITE
A reinforcing fiber in a resin matrix whose cumulative properties are superior to the individual materials.
COMPOUND
An intimate admixture of (a) polymer(s) with all the materials necessary for the finished product.
COMPRESSION MOLD
A closed mold, usually of steel, used to form a composite under heat and pressure.
COMPRESSIVE MODULUS
A mechanical property description which measures the compression of a sample at a specified load. Described in ASTM D-695.
COMPRESSIVE STRENGTH
The stress a given material can withstand when compressed. Described in ASTM-D 695.
CONDENSATION POLYMER
A polymer made by condensation polymerization.
CONDENSATION POLYMERIZATION
Polymerization in which monomers are linked together with the splitting off of water or other simple molecules.
CONNECTION
Where two panels are attached to each other or a panel is attached to the building.
CONTACT MOLDING
Refers to the use of a single or open mold onto which resin and reinforcement materials can be applied. Contact molding is characterized by one finished cosmetic side.
CONTINUOUS FILAMENT STRAND
A fiber bundle composed of many glass filaments. Also when referring to gun roving; a collection of string like glass fiber or yarn, which is fed through a chopper gun in the spray up process.
CONTINUOUS STRAND ROVING
A bundle of glass filaments which are fed through a chopper gun in the spray up process.
CONTINUOUS LAMINATING
An automated process for forming panels and sheeting in which fabric or mat is passed through a resin bath, brought together between covering sheets, and passed through a heating zone for cure. Squeeze rolls control thickness and resin content as the various plies are brought together.
COOLING TIME
In molding the time interval from the start of forward screw movement until the mold starts to open.
CORE
A low density material used between two FRP skins. Examples of core materials are end-grain balsa wood, urethane foam, PVC foam and various honeycomb materials.
CRACK
An actual separation of the laminate, visible on opposite surfaces, and extending through the thickness.
CRACK SURFACE
Crack existing only on the surface of the laminate.
CRATER
A small shallow surface imperfection.
CRAZING
Cracking of gel coat or resin due to stress.
CREEP
The time dependent part of strain resulting from stress.
CRITICAL AREA
An area in which the presence of imperfection is considered to be most detrimental. The areas of the parts that are critical structurally, aerodynamically, or electrically shall be uniform.
CROSS LAMINATE
A laminate in which some of the layers of material are oriented approximately at right angles to the remaining layers with respect to the grain or strongest direction in tension.
CROSS-LINKING
The chemical bonding of molecules which in polymers occurs in the curing transition from a liquid to a solid.
CROSS SECTION OF THE CAVITY
In a mold for test specimens, the area of a planar section perpendicular to the flow pattern during filling of the mold that forms the critical portion of the test specimen.
CURE
The completion of the cross-linking process during which a composite develops its full strength.
CURE CYCLE
The schedule of time periods, at specified conditions, to which a reacting thermosetting material is subjected to reach a specified property level.
CURE TIME
Time between introduction of catalyst or initiator to a polymer and final cure.
CURING AGENTS
Materials used to initiate the polymerization of a resin. The catalyst is the primary agent. Promoters and accelerators are secondary or assisting agents.
CUT EDGE
End of a laminate resulting from cutting that is not protected by a corrosion barrier.
CUT LAYERS
As applied to laminated plastics, a condition of the surface of machined or ground rods and tubes and of sanded sheets in which cut edges of the surface layer or lower laminations are revealed.
CYCLE TIME
In molding the total time used to carry out a complete sequence of operations making up the molding cycle.
DEGRADATION
A deleterious change in the chemical structure, physical properties, or appearance of a plastic.
DEGRADABLLE PLASTICS
A plastic designed to undergo a significant change in its chemical structure under specific environmental conditions resulting in a loss of some properties that may vary as measured by standard test methods appropriate to the plastic and the application in a period of time that determines its classification.
DELAMINATION
The separation of composite layers from each other.
DENSITY
A comparison of weight per volume, measured in pounds per cubic foot.
DEPTH
In the case of a beam, the dimension parallel to the direction in which the load is applied.
DIELECTIC STRENGTH
The value of a material as an electrical insulator or the resistance to the flow of electric current.
DIMENSIONAL STABILITY
A description of the change in size of an object during the molding process or in varying temperature conditions or under various loads.
DISHED END
Radiused end closure for a cylindrical vessel, as opposed to a flat or coned area.
DISTORTION
A change in shape form that which is intended.
DOME
In reinforced plastics, an end of a filament wound cylindrical container.
DRAFT
The angle of the vertical components of a mold which allow removal of the part.
DRY BLEND
A dry compound prepared without fluxing or addition of solvent (also called powder blend).
DRY SPOT
An area where the reinforcement fibers have not been sufficiently wetted with resin.
DUROMETER
An instrument for measuring indentation hardness.
EDGE SEALING
Application of reinforcement and resin, or resin alone, to seal cut edges and provide a corrosion resistant barrier. The final layer of resin shall be paraffinated.
E-GLASS
Originally formulated for use in electric circuitry, E-glass is the most common glass formulation used in fiberglass reinforcements.
ELASTONER
A macromolecular material that at room temperature returns rapidly to approximately its initial dimensions and shape after substantial deformation by a weak stress and release of the stress.
ELONGATION
Standard measure for the amount a sample can stretch as a percentage of original length before it fails or breaks.
ENCAPSULATING
Completely surrounding an object with resin or a fiber resin composite.
ENGINEERED PLASTICS
A material that has been made by specific design and through use of particular monomers and monomer sequences to produce a plastic with desired properties, possibly for a specific application.
ENGINEERING PLASTICS
Those plastics and polymeric compositions for which well-defined properties are available such that engineering rather than empirical methods can be used fro the design and manufacture of products that require definite and predictable performances in structural applications over a substantial temperature range.
ENTRAPPED AIR VOID
Cavity in a laminate caused by a trapped gas bubble.
ENVIRONMENT
State of the surroundings in contact with the internal or external surface. Included are the temperature, pressure, chemical exposure, exposure to sunlight, relative to humidity, liquids, and / or gas.
EPOXY PLASTICS
Thermoplastic or thermosetting plastics containing ether of hydroxyalkyl repeating units, or both, resulting from the ring-opening reactions of lower molecular weight polyfunctional oxirane resins, or compounds, with catalysts or with various polyfunctional acidic or basic coreactants.
EPOXY RESIN
A polymer resin characterized by epoxide molecule groups.
EQUIPMENT
Vessels used for the storage, accumulation, or processing of corrosive or otherwise hazardous substances at pressure ranging from full vacuum to 15 psig.
EQUIPMENT ASSEMBLER
Person who puts together the component parts, e.g., joining sections, installation of nozzles, etc.
ETHYLENE PLASTICS
Plastics based on polymers of ethylene or copolymers of ethylene with other monomers, the ethylene being in greatest amount by mass.
EXOTHERMIC HEAT
Internally developed heat accompanying a chemical reaction, such as might be created when curing a thermosetting resin.
EXOTHERN PLY
That ply of chopped strand mat at which the lamination process is stopped to allow gelation and exothern of the existing laminate.
EXPANDABLE PLASTIC
A plastic in a form capable of being made cellular by thermal, chemical, or mechanical means.
EXTERIOR LAYER
Outer service area of a laminate.
EXTRUSION
A process in which heated or unheated plastic is forced through a shaping orifice (a die) in one continuously formed shape, as in film, sheet, rod, or tubing.
FABRICATING
The manufacture of plastic products from molded parts, rods, tubes, sheeting, extrusions, or other forms by appropriate operations such as punching , cutting, drilling, and tapping including fastening plastic parts together or to other parts by mechanical devices, adhesives, heat sealing or other means.
FABRICATOR
Manufacturer of reinforced plastic products.
FINITE ELEMENTAL ANALYSIS (FEA)
Finite element analysis (FEA) is a computer simulation technique used in engineering analysis. It involves dividing the area to be analyzed into finite elements (many small pieces with defined sizes), defining the boundary conditions (loads on the area being analyzed), and having the computer calculate the load interactions between all of the elements.
FEMALE MOLD
A concave mold used to precisely define the convex surface of a molded part.
FIBER
Reinforcement material which is a major component in a composite matrix.
FIBER GLASS
Glass which has been extruded into extremely fine filaments. These filaments vary in diameter, and are measured in microns. Glass filaments are treated with special binders and processed similar to textile fibers. These fibers come in many forms such as roving, woven roving, mat and continuous strands.
FIBERGLASS ROVING
A number of strands or filaments of glass fibers gathered together with little or no twist.
FIBERGLASS WOVEN ROVING
Heavy fabric woven from glass fiber rovings.
FIBER WETTING
Coating (wetting) of the fiberglass with resin by means of roll-out or immersion.
FIBER SHOW
Strands or bundles of fibers not covered by resin which are at or above the surface of a reinforced plastic.
FILAMENT
A single thread-like fiber of extruded glass. Typically microns in diameter.
FILAMENT WINDING
A process which involves winding a resin-saturated strand of glass filament around a rotating mandrel.
FILL PICKS
The rovings in a woven roving that run in the transverse direction of the fabric, i.e., across the roll width of the fabric.
FILLERS
Usually inert organic or inorganic materials which are added to plastics, resins or gel coats to vary the properties, extend volume, or lower the cost of the article being produced.
FILM
In plastics, an optional term for sheeting having a nominal thickness not greater than 0.25 mm (0.01 in.).
FIRE RETARDANTS
Compounds mixed with the resin to reduce flammability.
FISH EYE
The effect of surface contamination which causes a circular separation of a paint or gel coat.
FIT UP
The match between joining parts, elements or components.
FLAME RETARDANT RESIN
A polyester resin which has been specifically formulated to reduce the flame spread and/or smoke generation characteristics.
FLAMMABILITY
A measure of how fast a material will burn under controlled conditions. ASTM D-635/UL E-84 tests.
FLANGE
An extension around the perimeter of a mold or part for the purpose of demolding, stiffening or connecting two components.
FLASH POINT
The lowest temperature at which a substance gives off enough vapors to form a flammable mixture.
FLEXURAL MODULUS
ASTM D-790. An engineering measurement which determines how much a sample will bend when a given load is applied.
FLUOROCARBON PLASTIC
A plastic based on polymers made with monomers composed of fluorine, hydrogen, and carbon only.
FLUOROHYDROCARBON PLASTIC
Plastics based on polymers made with monomers composed of fluorine, hydrogen, and carbon only.
FLUOROPLASTIC
A plastic based on polymers made from monomers containing one or more atoms of fluorine, or copolymers of such monomers with other monomers, the fluorine containing monomers being in greatest amount by mass.
FOAM
A lightweight, cellular plastic material containing gas-filled voids. Typical foams include urethane, PVC and polyester.
FOAM-IN-PLACE
The process of creating a foam by the combination of two liquid polymers. See IN-SITU.
FOREIGN INCLUSION (metallic)
Metallic particles included in a laminate which are foreign to its composition.
FOREIGN INCLUSION (non-metallic)
Non-metallic particles of substance included in a laminate which seem foreign to its composition.
FORMING
A process in which the shape of plastic pieces such as sheets, rods, or tubes is changed to a desired configuration.
FRP
Fiber Reinforced Plastics, also known as GFRP (Glass Fiber Reinforced Plastic), GRP (Glass Reinforced Plastic), RP (Reinforced Plastic) and Composites.
FURAN PLASTICS
Plastics based on furan resins.
FURAN RESIN
A resin in which the furan ring is an integral part of the polymer chain and represents the greatest amount by mass.
GAP FILLING
The filling of voids between joined parts, elements, or components with resin putty or resin.
GATE
In an injection mold, a constriction in the flow channel between the runner and the mold cavity.
GEL
The irreversible point at which a polymer changes from a liquid to a semi-solid. Sometimes called the "B" stage.
GEL COAT
A surface coat of a specialized polyester resin, either colored or clear, providing a cosmetic enhancement and weatherability to a fiberglass laminate.
GEL TIME
The length of time from catalyzation to gel or "B" stage.
GELATION
The formation of a gel.
GLASS
An inorganic product of fusion which has cooled to a rigid condition with out crystallizing.
GLASS CONTENT
Weight percent of glass fiber reinforcement in the laminate.
GLASS FINISH
A material applied to the surface of glass fibers used to reinforce plastics and intended to improve the physical properties of such reinforced plastics over that obtained using glass reinforcement without finish.
GLASS TRANSITION TEMPERATURE
The approximate middle point of the temperature range over which the glass transition takes place.
GOOD SIDE
The side of a molding in contact with a mold surface.
GRAFT COPOLYMER
A copolymer in which polymeric side chains have been attached to the main chain of a polymer of different structure.
"GREEN"
Resin which has not completely cured and is still rather soft and rubbery.
GRP
Glass reinforced plastics. Generally based on polyester resin. See FIBERGLASS, FRP.
GUN ROVING
Fiberglass roving designed for use in a chopper gun for spray-up application.
GUSSET
A piece used to give additional size or strength in a particular location of an object.
HALOCARBON PLASTICS
Plastics based on resins made by the polymerization of monomers composed only of carbon and a halogen or halogens.
HAND LAY UP
The process of manually building up layers of fiberglass and resin using hand rollers, brushes and spray equipment.
HAZE
The cloudy or turbid aspect or appearances of an otherwise transparent specimen caused by light scattered from within the specimen or from its surface.
HEAT DISTORTION POINT
The temperature at which the strength of a material begins to degrade.
HEAT MARK
Extremely shallow depression or groove in the surface of a plastic visible because of a sharply defined rim or roughened surface.
HIGH DENSITY POLYETHLLENE PLASTICS (HDPE)
Those linear polyethylene plastics, g. v., having a standard density of 0.941 g/cm3 or greater.
HIGH PRESSURE MOLDING
A method of molding or laminating in which the pressure used is greater than 1400 kPa (200psi).
HELICAL WINDING
Filament winding where the reinforcement is places at some angle (other than 0 deg or 90 deg) to the axis of rotation.
HET-ACID RESIN
Polyester resin with exceptional fire qualities.
HOMOPOLYMER
A polymer resulting from polymerization involving a single monomer.
HOT PATCH
Several small fiberglass mat tabs, saturated with highly catalyzed resin, used to hold butted or joined parts or components in preparation for bonding.
HONEYCOMB CORE
Strips of paper, plastic, metal, etc., joined together to form a honeycomb pattern. Used as a lightweight core in sandwich moldings.
HYDROCARBON PLASTICS
Plastics based on resins made by the polymerization of monomers composed of carbon and hydrogen only.
HYDROLYTICALLY DEGRADABLE PLASTIC
A degradable plastic in which the degradation results from hydrolysis.
HYDROSTATIC TEST
Pressure test of equipment using water as the test medium.
IMPREGNATE
To saturate with resin. The most common application is saturating fiberglass with a catalyzed resin.
INDEPENDENT TESTING LABORATORY
The laboratory conducting the tests require by RTP-1 must be an entity separate organizationally, legally, and financially, from the Fabricator and User or Userís Agent. Additionally, no commercial, financial, or individual relationships shall exist between the parties that might compromise efforts to produce and report accurate test results. It is expected, however, that a commercial purchase order, contract or agreement will be employed by the parties to arrange for testing services. The independent testing laboratory must be equipped and staffed with the necessary skilled personnel to conduct the tests in accordance with the requirements of the Standard.
INHIBITOR
An additive to polyester resin or styrene used to slow the chemical reaction which leads to curing.
INJECTION MOLDING
The process of forming a material by forcing it, in a fluid state and under pressure, through a runner system (sprue, runner, gate(s)) into the cavity of a closed mold.
INJECTION TIME
The time interval from the beginning of screw forward movement until switching over to hold pressure.
INSERT
A piece of material put into a laminate during or before molding to serve a definite purpose.
INTERSPERSE
Chopped fiberglass used in a filament wound laminate, usually in thin layers between winding coverages.
INTUMESCENT
A fire-retardant technology which causes an otherwise flammable material to foam, forming an insulating barrier when exposed to heat.
IN-SITU
In the position which it will finally occupy, e.g. molding or forming foam.
ISOPHTHALIC
A polyester resin based on isophthalic acid, generally higher in properties than a general purpose or orthothatic polyester resin.
ISOPTROPIC
The description of equal strength properties in all orientation. Isoptropic composites are usually achieved by random fiber orientation.
ISOTACTIC
Pertaining to a type of polymeric molecular structure containing a sequence of regularly spaced asymmetric atoms arranged in like configuration in a polymer chain.
JACKSTRAWING
A visual effect of glass fiber turning white in a cured laminate. This usually does not affect the strength of a laminate, but could be an indication of materials incompatibility.
JIG
Any fixture for holding parts in position, while joining them together or to maintain their shape.
JOINT
A line or distinction formed when two panels are connected. Also referred to as a seam.
JOINT OVERLAY
An overlay laminate that joins the adjoining surfaces of two contacting parts or elements.
KNUCKLE AREA
In reinforced plastics, the area of transition between sections of different geometry in a filament wound part.
LACK of FILLOUT
An area, occurring usually at the edge of a laminated plastic, where the reinforcement has not been wetted with resin.
LAMINANT
The product of lamination. A composite consisting of a layer or layers of thermoset polymer and fiber reinforcement.
LAMINATE
To place into a mold a series of layers of polymer and reinforcement. The process of applying FRP materials to a mold.
LAMINATION
Applying layers of glass and resin to a mold. Also used to describe a single ply of laminate.
LAMINATE COMPOSITION
The sequence of reinforcement materials on a type, class, and category basis that make up a laminate.
LAMINATE ELEMENT
A part of the structural layer of a filament wound laminate that is described by the wind angle, number of coverages with supplementary reinforcement ( if used ), and the required sequence.
LAMINATION ANALYSIS
Procedure by which, given the amount and properties of the resin and the properties and orientation of the reinforcement, it is possible to calculate the elastic properties of the individual layers and the total laminate.
LATTICE PATTERN
In reinforced plastics, a pattern of filament winding with a fixed arrangement of open voids.
LAY
The length of twist produced by stranding filaments, such as fibers, wires or roving.
LAY OUT
The arrangement and location of parts, elements, and/or components that reflect the design of a product.
LAYER
A single ply of lay up or laminate.
LAY UP
The act of building up successive layers of polymer and reinforcement. Layers of catalyzed resin and fiberglass or other reinforcements are applied to a mold in order to make a part.
LET GO
An area in laminated glass over which an initial adhesion between interlayer and glass has been lost.
LIGIN PLASTICS
Plastics based on ligin resins.
LIGIN RESIN
A resin made by heating ligin or by reaction of ligin with chemicals or resins, the ligin being in greatest amount by mass.
LINEAR LOW DENSITY POLYETHYLENE PLASTICS
Those linear polyethylene plastics, q v., having a standard density of 0.919 to 0.925 g/cm3
LINEAR MEDIUM DENSITY POLYETHYLENE PLASTICS
Those linear polyethylene plastics, q. v., having a standard density of 0.926 to 0.940 g/cm3.
LINEAR POLYETHYLENE PLASTICS
Those containing insignificant amounts of long chain branching which may contain significant amounts by design, of short chain branching.
LOW DENSITY POLYETHYLENE PLASTICS
Those branched polyethylene plastics, q. v. , having a standard density of 0.910 to 0.925 g/cm3.
LOW-PRESSURE LAMINATES
Laminated, molded and cured using pressures from 400 psi down to and including the pressure obtained by the mere contact of the plies.
LOW PRESSURE MOLDING
A method of molding or laminating in which the pressure is 1400kPa (200psi) or less.
LUMINOUS TRANSMITTANCE
The ratio of the luminous flux transmitted by a body to the flux incident upon it.
MALE MOLD
A convex mold where the concave surface of the part is precisely defined by the mold surface.
MANDREL
Mold around which a laminate is formed to fabricate a cylindrical section.
MANUFACTURERS
Producers of materials of construction, e.g., resin reinforcement fibers, catalysts, common additives, etc.
MANWAY
Large nozzle or opening in a vessel for the purpose of entry by personnel.
MASTER (plug)
A full scale representation of the intended part, usually retained as a reference and the part from which production molds are made.
MAT
See CHOPPED STRAND MAT.
MATCHED DIE MOLDING
Technique for producing long runs of identical parts with two finished sides.
MATCHED MOLDS
Two or more tools arranged in a set as a male and female mold. Normally used in a press.
MATRIX
The liquid component of a composite or laminate.
MECHANICALLY FOAMED PLASTIC
A cellular plastic in which the cells are formed by the physical incorporation of gas.
MEDIUM DENSITY POLYETHYLENE PLASTICS
Those branched polyethylene plastics, q. v., having a standard density of 0.926 to 0.940 g/cm3.
MEK PEROXIDE (MEKP)
An initiator often referred to as catalyst and used to initiate polymerization of a resin. Methyl Ethyl Ketone Peroxide.
MEK SOLVENT
Methyl Ethyl Ketone; a colorless, flammable liquid sometimes used in clean up procedures.
MELAMINE PLASTICS
Plastics based on resins made by the condensation of melamine and aldehydes.
MELT PRESSURE
The pressure applied to the plastic material in front of the screw driving the injection molding process on a reciprocating screw machine that is calculated based on the hydraulic force acting axially on the screw.
MELT TEMPERATURE
The temperature of the molten plastic.
MICROBALLOONS
Microscopic bubbles of glass, ceramic or phenolic, used as a filler or to create syntactic foam or putty mixtures.
MIL (MIL THICKNESS)
The unit used in measuring film thickness. One mil equals one thousandth of an inch. (l mil = .001 ").
MILLED FIBERS
Glass fiber processed by a hammer mill into lengths of 1/32" to 1/8". Commonly used as a reinforcement in polyester putty.
MODULUS OF ELASTICITY
An engineering term used to describe a material's ability to bend without losing its ability to return to its original physical properties.
MOLD
The tool used to fabricate the desired part shape. Also used to describe the process of making a part in a mold.
MOLDING
The process of using a mold to form a part.
MOLD OPEN TIME
The time interval from the instant the mold begins to open until it is closed again.
MOLD RELEASE
A wax or polymer compound that is applied to the mold surface which acts as a barrier between the mold and the part, thus preventing the part from bonding to the mold.
MOLD TEMPERATURE
The mean temperature of the mold cavity surface measured after the system has obtained thermal equilibrium and immediately after opening the mold.
MOLD PRESSURE, COMPRESSION
The calculated fluid pressure applied to the material in the mold.
MOLD PRESSURE INJECTION
The pressure applied to the cross-sectional area of the material cylinder.
MOLDING PRESSURE TRANSFER
The pressure applied to the cross sectional area of the material pot or cylinder.
MONOMER
One of the constituents of polyester resin.
MSPI
Manufacturerís Specific Product Identification.
NPG GEL COAT
Neopentyl glycol gel coat has enhanced weatherability compared to non-NPG gel coat.
NECKING
The localized reduction in cross section which may occur in a material under tensile stress.
NONRIGID PLASTIC
For purposes of general classification , a plastic that has a modular elasticity either in flexure or in tension of not over 70 MPa (10 000psi) at 23 degree C and 50% relative humidity when tested in accordance Test Methods D 790, Test Method D 747, Test Method D 638, or Test Methods D 882.
NOVOLAC (OR NOVOLAK)
A phenolic-aldehyde resin which, unless a source of methylene groups is added, remains permanently thermoplastic.
NYLON PLASTICS
Plastics based on resins composed principally of long chain synthetic polymeric amide which has recurring amide groups as an integral part of the main polymer chain.
OLEFIN PLASTICS
Plastics based on polymers made by the polymerization of olefins or copolymerization of olefins with other monomers, the olefins being at least 50 mass %.
OLIGOMER
A substance composed of only a few nonomeric units repetitively linked to each other, such as a dimer, trimer, tetramer, etc, or their mixtures.
OLIGOMERIZATION
The process of converting a monomer or mixture of monomers into an oligomer.
OPEN-CELL CELLULAR PLASTIC
A cellular plastic in which there is a predominance of interconnected cells.
ORANGE PEEL
A gel coated or painted finish which is not smooth and is patterned similar to an orange's skin.
ORGANOSOL
A suspension of finely divided polymer in a plasticizer, together with a volatile organic liquid.
ORTHOPHTHALIC OR ORTHO RESIN
A polyester resin based on orthophthalic acid, also known as a general purpose resin (GP).
OVERLAY
Laminates used over base RTP structures to secure a joint, seal a seam, attach a nozzle, etc.
OXIDATIVELY DEGRADABLE PLASTIC
A degradable plastic in which the degradation results from oxidation.
PARAFFINATED RESIN
Resin containing a small amount of dissolved paraffin (usually 0.1% to 0.5 %). Polymerization of polyesters is inhibited by contact with the atmosphere. During cure, the paraffin migrates to the surface, sealing it against atmospheric exposure.
PARALLEL LAMINATE
A laminate in which all the layers of material are oriented approximately parallel with respect to the grain or strongest direction in tension.
PARISON
The shaped plastic mass, generally in the form of a tube, used in blowing molding.
PARTING AGENT
See MOLD RELEASE and PVA.
PARTING LINE
The location on a molded product between different segments of the mold used to produce the product.
PATTERN
The initial model for making fiberglass molds. See PLUG.
PHENOLIC PLASTICS
Plastics based on resins made by the condensation of phenol, such as phenol or cresol, with aldehydes.
PHENOLIC RESIN COMPOUND, SINGLE STAGE
A phenolic material in which the resin , because of its reactive groups, is capable of further polymerization by application of heat.
PHENOLIC RESIN COMPOUND, TWO-STAGE
A phenolic material in which the resin is essentially not reactive at normal storage temperatures, but contains a reactive additive , which causes further polymerization upon the application of heat.
PHOTODEGRADABLE PLASTIC
A degradable plastic in which the degradation results from the action of normal daylight.
PIGMENT
A colorant added to gel coat or resin.
PIGMENT SEPARATION
Occurs when the pigment is not thoroughly mixed into the gel coat during formulation or the gel coat is improperly mixed prior to use. It is characterized by a nonhomogeneous surface color.
PIMPLE
Small, sharp or conical elevation on the surface of a laminate.
PINHOLES
Small holes on the exposed gel coated surface. They are about the diameter of common pins and may be easily counted.
PIT
Small crater in the surface of the laminate.
PLASTICS
Organic chemical compounds called polymers which can be formulated to produce a wide range of properties.
PLASTICIZER
A substance incorporated in a material to increase its workability, flexibility, or distensibility.
PLASTIC PIPE
A hollow cylinder of plastic material in which the wall thicknesses are usually small when compared to the diameter and in which the inside and outside walls are essentially concentric.
PLASTIC TUBING
A particular size of plastic pipe in which the outside diameter is essentially the same as the corresponding size of copper tubing.
PLASTISOL
A liquid suspension of a finely divided PVC polymer or copolymer in a plasticizer.
PLATE MARK
Any imperfections in a pressed plastics sheet resulting from the surface of the pressing plate.
PLUG
A composite industry term for a pattern or model.
POLEPIECE
In reinforced plastics, the supporting part of the mandrel used in filament winding, usually on one of the axes of rotation.
POLYARYLETHERKETONE
A polymer in which aryl groups are connected by one or more ether as well as one or more Ketone linkages.
POLYBUTYLENE
A polymer prepared by the polymerization of butene as the sole monomer.
POLYBUTYLENE PLASTICS
Plastics based on polymers made with butane as the sole monomer.
POLYCARBONATE
A polyester polymer in which the repeating structural units in the chain is of the carbonate type.
POLYCARBONATE PLASTICS
Polyester plastics based on polymers in which the t repeating structural units in the chains are essentially all of the carbonate type.
POLYDICYCLOPENTADIENE PLASTIC
A cross linked thermoset polymer formed by the ring opening metathesis polymerization of dicyclopentadiene.
POLYESTER RESIN (Unsaturated)
The product of an acid-glycol reaction commonly blended with a monomer to create a polymer resin. In its thermosetting form it is the most common resin used in the FRP industry.
POLYETHER
A polymer in which the repeated structural unit in the chain is one of the ether type.
POLYETHYLENE
A polymer prepared by the polymerization of ethylene as the sole monomer.
POLYETHYLENE PLASTICS
Plastics based on polymers made with ethylene as essentially the sole monomer.
POLYMER
A chain molecule composed of many identical groups, commonly found in plastics.
POLYMERIZATION
The chemical bonding of polymer molecules during the curing reaction.
POLYMETHYLMETHACRYLIMIDE
A thermal plastic polymer formed from a reaction of poly (methyl methacrylate ) and monomethyl amine.
POLYOL
An alcohol having many hydroxyl groups, also known as a polyhydric alcohol or polyalcohol.
POLYOLEFIN
A polymer prepared by the polymerization of an olefin(s) as essentially the sole monomer(s).
POLYOLEFIN PLASTIC
Plastics based on polymers made with an olefin(s) as essentially the sole monomer(s)
POLYOXYMETHYLENE
A polymer in which the repeated structural unit in the chain is oxymethylene.
POLYOXYMETHYLENE PLASTICS
Acetal plastics based on polymers in which oxymethylene is essentially the sole repeated structural unit in the chains.
POLYPHTHALAMIDE (PPA)
A polyamide in which residues of terephthalic acid or isophthalic acid or a combination of the two comprise at least 60molar percentage of the dicarboxylic acid part of the repeating structural units in the polymer chain.
POLYPROPYLENE
A polymer prepared by the polymerization of propylene as the sole monomer.
POLYPROPYLENE PLASTICS
Plastics based on polymers made with propylene as essentially the sole monomer.
POLYSTYRENE
A polymer prepared by the polymerization of styrene as the sole monomer.
POLYTEREPHTHALATE
A thermoplastic polyester in which the terephthalate group is one of the repeating structural unit in the polymer chain.
POLYTEREPHTHALATE PLASTICS
A thermoplastic polyester in which the terephthalate group is one of the repeating structural unit in the polymer chain.
POLYURETHANE
A polymer prepared by the reaction of an organic diisocyanate with compounds containing hydroxyl groups.
POLY (VINYL ACETATE)
A polymer prepared by the polymerization of vinyl acetate as the sole monomer.
POLY (VINYL CHLORIDE)
A polymer prepared by the polymerization of vinyl chloride as the sole monomer.
POSTFORMING
The forming of cured or partially cured thermosetting plastics.
POLYVINYL ALCOHOL (PVA)
A parting film applied to a mold for part releasing.
POROSITY
Entrapped gas bubbles or voids in a gel coat film.
POST-CURE
To cure by application of heat after the chemical exothermic reaction has subsided.
POT LIFE
The time during which the catalyzed resin remains liquid or "workable." See GEL TIME.
PREFORM
A coherent, shaped mass of powdered, granular or fibrous plastic molding compound, or fibrous filler material with or without resin.
PRE-GEL
An unintentional extra layer of cured resin on part of the surface of the laminate.
PREMIX
Reinforcing material mixed with resin, and usually with pigment, filler and catalyst, before placing in the mold.
PREPOLYMER
A polymer of degree of polymerization between that of the monomer or monomers and the final polymer.
PREPREG
Reinforcing material impregnated with resin prior to the molding process and cured by the application of heat.
PRESSURE BAG
A membrane which conforms to the inside of a laminate laid up on a mold. The membrane or bag is then inflated applying pressure which consolidates and densifies the laminate.
PRESSURE BREAK
As applied to a defect in a laminated plastic a break apparent in one or more outer sheets of the paper, fabric, or other base visible through the surface layer of resin which covers it.
PRINT THROUGH
A distortion in the surface of a part which allows the pattern of the core or fiberglass reinforcement to be visible through the surface. Also known as print out, telegraphing or read through.
PROMOTER
A reagent which speeds resin cure. See ACCELERATOR.
PROFILE
The roughness (smoothness) of the surface.
PROPYLENE PLASTICS
Plastics based on polymers of propylene or copolymers of propylene with other monomers, the propylene being the greatest number in mass.
PULLED SURFACE
As applied to a defect in a laminated plastic imperfections in the surface ranging from a slight breaking or lifting in spots to pronounced separation of its surface from its body.
PUTTY
A thickened mixture of resin made by adding fillers, thixotrophs and reinforcing fibers.
PVA
See POLYVINYL ALCOHOL.
QUALITY ASSURANCE
The system by which the Fabricator provides evidence that the quality control system has been followed in the construction of the product.
QUALITY CONTROL
The system a Fabricator uses to fabricate the equipment in compliance with this standard.
RECYCLED PLASTIC
Those plastics composed of post consumer material or recovered material only, or both, that may or may not have been subject to additional processing steps of the types used to make products such as recycled ñregrind or reprocessed or reconstituted plastics.
REGULAR TRANSMITTANCE
Ratio of the light flux transmitted without diffusion to the flux incident.
REFEREE SAMPLES
Laminate specimens submitted to establish a level of quality for judging acceptance/rejection of production equipment.
REINFORCED MOLDING COMPOUND
Compound consisting of a polymer and a reinforcement fiber or filler supplied by raw material producer in the form of ready-to-use materials.
REINFORCED PLASTIC
A plastic with high strength fillers imbedded in the composition, resulting in some mechanical properties superior to those of the basic resin.
REINFORCEMENT
A fiber which when encapsulated in a polymer resin matrix forms a composite or fiberglass laminate. Also refers to a structural member designed to stiffen a molded part.
RELEASE AGENT
A compound used to reduce surface tension or adhesion between a mold and a part.
RELEASE FILM
Film used to facilitate removal of the part from the mold or mandrel. Oriented polyester film, 3-5 mil (Mylar, Types A,S.or D; or Melinex11, Types S,O, or 442), has been found suitable for this purpose.
REPAIRABLE DEFECTS
Reparable defects, if any, shall consist of those which can be repaired without affecting the serviceability of the part unless prohibited in the product drawing or in the contract.
REPROCESSED PLASTIC
A thermoplastic prepared from usually melt processed scrap or reject parts by a plastics processor, or from non-standard or non-uniform virgin material.
RESIN
A liquid polymer which when catalyzed cures to a solid state.
RESIN POCKET
An apparent accumulation of excess resin in a small localized area within the laminate.
RESIN PUTTY
Resin filled with clay, fumed silica, milled glass fibers, or other inert materials to provide putty like consistency.
RESIN RICH EDGE
Insufficient reinforcing material at the edge of laminate molding.
RESIN RICH LAYER
Term often used to describe the corrosion barrier. The term does not imply excessive resin content.
RESIN RICHNESS
Excessive amounts or uneven distribution of resin in the laminate . Such areas are subject to cracking. Resin richness is the result of improper wet-out procedures as well as inadequate or improper roll-out techniques or drainage.
RESIN STREAK
A streak of excess resin on the surface of a laminated plastic.
RESIN TEARING
Separation of pigments in a gel coat affecting cosmetic appearance.
REWORKED PLASTIC
Plastic from a processorís own production that has been reground, palletized, or solvated after having been previously processed by molding , extrusion, etc.
RIGID PLASTIC
For purposes of general classification, a plastic that has a modulus of elasticity, either in flexure or in tension, greater than 700MPa (100 000 psi) at 23 degrees C 50 % relative humidity when tested in accordance with Test Method D 747, Test Methods D 790, Test Method D638, or Test Methods D 882.
ROLL OUT
Densification of the laminate by working reinforcement into the resin and the air out of the resin using a roller (a separate metal or thermoplastic roller is often used for this purpose).
ROUGH PROFILE
The result of sanding , machining , or otherwise abrading a laminate surface to produce a roughened surface for bonding.
ROVING
A collection of bundles of continuous filaments in untwisted strands. Used in the spray-up (chopping) process.
RTP
Reinforced Thermoset Plastic
RUBBER
A material that is capable of recovering from large deformations quickly and forcibly, and can be, or already is, modified to a state in which it is essentially insoluble (but it can swell) in boiling solvent, such as benzene, methylethylketone, and ethanol-toluene azeotrope.
RUNNER
The secondary feed channel in an injection or transfer mold that runs from the inner end of the sprue or pot to the cavity gate.
SAMPLE
A small part or portion of a material or product intended to be a representative of the whole.
SANDWICH CONSTRUCTION
A laminate with two composite skins separated by, but bonded to, a structural core material. Used to create stiff, lightweight structures.
SCRATCH
Shallow mark, grove, furrow or channel.
SECONDARY BOND STRENGTH
Adhesive force that holds a separately cured laminate to the basic substrate laminate.
SEAM
See JOINT.
SELF EXTINGUISHING
Ceases to burn when the source of flame is removed.
SELF-TAPPING SCREWS
Hardened screws which cut their own thread as they are set.
SET
Strain remaining after complete release of the force producing the deformation.
SHEET
An individual piece of sheeting.
SHEETING
A form of plastic in which the thickness is very small in proportion to length and width and in which the plastic is present as a continuous phase throughout, with or without filler.
SHEET MOLDING COMPOUND
A fiber reinforced thermosetting compound.
SHORT
In a laminate an incompletely filled out condition.
SHOT VOLUME
The total hollow space of a mold including cavity or cavities, runner(s) and sprue.
SLUGS
Unfiberized beads of glass.
SHEAR
An engineering term referring to forces applied normal to the surface of a given material. The movement between plies of a laminate is referred to as interlaminate shear.
SHELF LIFE
The allowable storage time before a product must be used.
SHIP LAP
Method of joining two panels together by means of one panel having a recessed shelf to receive the other panel on top of it leaving a flush surface.
SHRINK MARK (sink)
Depression in the surface of a molded laminate where it has retracted from the mold.
SILICONE PLASTICS
Plastics based on polymers in which the main polymer chain consists of alternating silicone and oxygen atoms.
SKIN COAT
The first layer of laminate next to the gel coat, generally, one ply of chopped strand mat.
SPECIFIC GRAVITY
The ratio between the density of a given substance and the density of water.
SPECIMEN
A piece or portion of a sample used to make a test.
SPLIT MOLD
An open mold made in two or more pieces.
SPRAY UP
The process of spraying glass fibers, resin and catalyst simultaneously into a mold using a chopper gun.
SPRUE
The primary feed channel that runs from the outer face of an injection or transfer mold to the mold gate in a single cavity mold.
STRAIN
Elongation per unit length.
STRAND
A plurality of filaments gathered together and bound by sizing.
STRESS
Load per unit area.
STRESS CRACK
An external or internal crack in a plastic caused by tensile stresses less than its short time mechanical strength.
STRUCTURAL LAYER
The portion of the laminate construction providing the primary mechanical strength.
STYRENE MONOMER
A component of polyester resin that provides crosslinking sites and reduces the polyester to a workable viscosity.
STYRENE PLASTICS
Plastics based on polymers of styrene or copolymers of styrene with other monomers, the styrene being in greatest amount by mass.
STYRENE RUBBER PLASTICS
Plastics based on styrene polymers and rubbers, the styrene polymers being in the greatest amount by mass/
STYRENIC THERMOPLASTIC ELASTONER
A copolymer material comprising styrenic end block segments bound to a rubbery segment that may be saturated or unsaturated.
SURFACE PREPARATION
The act of roughening, priming, or otherwise treating laminate surfaces to achieve surface conditions that are conductive to adhesion of subsequently applied bonds.
SURFACING MAT
A lightweight tissue (10-30 mils thick) of glass or synthetic fiber used to provide a resin-rich surface. See VEIL.
SURFACTANT
Chemicals used to modify or change the surface of a layer of resin or polymer. Usually used to form a film on a curing resin, producing a tack-free surface.
SYNERESIS
The contraction of a gel accompanied by the separation of a liquid.
SYNTACTIC CELLULAR PLASTICS
Materials consisting of hollow sphere fillers in a resin matrix.
SYNTACTIC FOAM
A foam made by mixing microspheres with a resin.
TACK FREE
A surface which is not sticky after cure.
TAPE
A narrow width reinforcing fabric or mat.
TELOMER
A polymer composed of molecules having terminal groups incapable of reacting with additional monomers, under the conditions of the synthesis, to form larger polymer molecules of the same chemical type.
TENSILE LOAD
A dulling load applied to opposite ends of a given sample.
TENSILE ELONGATION
An engineering term referring to the amount of stretch a sample experiences during tensile strain. ASTM D-638.
TENSILE STRENGTH
A measurement of the tensile load a sample can withstand. ASTM D-638.
TEX
Linear density of roving expressed in grams per 1 000m.
THERMAL BREAK
A solid or cellular material or combination of materials of low thermal transmission placed between components of high thermal transmission in order to reduce the heat flow across assembly.
THERMAL COEFFICIENT OF EXPANSION
Measures dimensional change of a material when heated or cooled. Measured in inches per inch per degree.
THERMAL CONDUCTIVITY
Measures the transfer of heat through a material.
THERMALLY FOAMED PLASTIC
A cellular plastic produced by applying heat to effect gaseous decomposition or volatilization of a constituent.
THERMOPLASTIC ELASTOMERS (TPE)
A diverse family of rubber like materials that , unlike conventional vulcanized rubbers, can be processed and recycled like thermoplastic materials.
THERMOPLASTICS
A group of plastic materials that become elastic or melt when heated, and return to their rigid state at room temperature. Examples are PVC, ABS, polystrene, polycarbonates, nylon, etc.
THERMOSETS
Materials that undergo a chemical crosslinking reaction going from liquid to solid or semi-solid. This reaction is irreversible. Typical thermosets are polyesters, acrylics, epoxies, and phenolics.
THERMOSETTING
Capable of being changed into a substantially infusible or insoluble product when cured by heat or other means.
THIXOTROPIC
A term describing the rehology (or flow characteristics) of a liquid that resists flowing or drainage during application.
THIXOTROPIC INDEX (T.I.)
A measure of thixotropy using a Brookfield Viscometer. The low speed viscosity divided by the high speed viscosity.
TOOLING GEL COAT
A gel coat formulated for mold surfaces.
TRANSLUCENT
Permits a percentage of light to pass but not optically clear like window glass.
TRANSFER MOLDING
A method of forming articles by fusing a plastic material in a chamber and than forcing essentially the whole mass into a hot mold where it solidifies.
TRANSITION, FIRST ORDER
A change of state, associated with crystallization or melting in a polymer.
UNDERCUT
An area of a part or mold that has an acute angle between two surfaces. If a part has an undercut a split mold is necessary.
UNIDIRECTIONAL
Strength lying mainly in one direction. A glass reinforcement in which the fiber is oriented in one direction.
UREA PLASTICS
Plastics based on resins made by the condensation of urea and aldehydes.
URETHANE PLASTICS
Plastics based on polymers in which the repeated structural units in the chains are of the urethane type, or on copolymers in which urethane and other types of repeated structural units are present in the chains.
USER
Organization for which the equipment is being fabricated.
UV ABSORBER
Compounds that are added to resins to enhance their ultraviolet resistance.
UV STABILIZER
A chemical compound which improves resistance to degradation from ultraviolet radiation.
VINYL ACETATE PLASTICS
Plastics based on polymers of vinyl acetate or copolymers of vinyl acetate with other monomers, the vinyl acetate being in greatest amount by mass.
VINYL CHLORIDE COPOLYMER
A polymer prepared by the polymerization of vinyl chloride and other monomers, the vinyl chloride content being a minimum 51% of the mass of the polymer.
VINYL CHLORIDE PLASTICS
Plastics based on polymers of vinyl chloride or copolymers of vinyl chloride with other monomers, the vinyl chloride being in greatest amount by mass.
VACUUM BAG MOLDING
Process for eliminating voids and forcing out entrapped air and excess resin from lay ups by drawing a vacuum from a plastic film which blankets a laminate.
VINYL ESTER RESIN
Resin characterized by reactive unsaturation located predominately in terminal positions which can be compounded with styryl monomers and reacted to give highly cross-linked thermoset copolymers.
VINYLIDENE CHLORIDE PLASTICS
Plastics based on polymer resins made by the polymerization of vinylidene chloride or copolymerization of vinylidene chloride with other unsaturated compounds, the vinylidene chloride being in the greatest amount by weight.
VIRGIN PLASTICS
Plastic material in the form of pellets, graules, powder, floc, or liquid that has not been subjected to use or processing other than that required for its initial manufacture.
VISCOSITY
The liquid properties of a material. Resistance to flow.
VISCOSITY COEFFICENT
The shearing stress necessary to induce a unit velocity flow gradient in material.
VOID FREE
A molding containing no entrapped air cavities, blisters, or voids.
VOIDS
Unfilled space caused by air or gas in the resin mix or by entrapment of such gases during lay-up of individual piles of glass. Excessive voids reduce the strength and chemical resistance of the laminate, particularly if the voids are at the resin glass interface.
VULCANIZATION
An irreversible process during which a rubber compound, through a change in its chemical structure (for example cross-linking), becomes less plastic and more resistant to swelling by organic liquids and elastic properties are conferred, improved or extended over a greater range of temperature.
WARP ENDS
The roving in a woven roving that runs in the longitudinal direction of the fabric, i.e. , along the roll length of the fabric.
WARPAGE
Distortion caused by nonuniform change of internal stresses.
WASH
Area where the reinforcement of molded plastic has moved inadvertently during closure of the mold resulting in resin-rich areas.
WATER ABSORPTION
The amount of water which a laminate will absorb.
WAX
A compound used as a release agent. See RELEASE AGENT.
WELD OR KNIT-LINE
A mark on, or weakness, in a molded plastic formed by the union of two or more streams of plastic flowing together.
WELD-LINE
A discontinuity in a molded plastic part formed by the merging of two or more streams of plastic flowing together.
WELD MARK
A visible weld-line.
"WET-OUT"
The action of saturating a glass fabric with resin. Also a measure of the speed with which a fabric soaks up resin.
WET WINDING
A method of making filament-wound reinforced plastics in which the fiber reinforcement is coated with a polymer compound as a liquid just prior to wrapping on a mandrel.
WHISKER
A short, single-crystal fiber.
WIDTH
In the case of a beam, the cross-sectional dimension perpendicular to the direction in which the load is applied.
WIND ANGLE
Angle from the axis of rotation at which the reinforcement strands are placed in the filament winding process.
WIND CYCLE
In filament winding, one traversing of the carriage to the end of the mandrel and return to the original position. Depending on band width, part diameter, and wind angle, one or more wind cycles will be needed to achieve one coverage.
WORMHOLE
Elongated air entrapment which is either in or near the surface of the laminate and may be covered by a thin film of cured resin.
WOVEN ROVING FABRIC
Heavy fabrics woven from continuous filament in roving form. Usually in weights between 18-30 oz. per square yard.
WRINKLES
In a laminate an imperfection that has the appearance of a wave molded into one or more piles of fabric or other reinforcement materials.
YARN
Twisted strands of roving used to weave textile reinforcements.
YIELD
Linear density of roving expressed in yards per pound.